Grasping the Art of Welding: How to Prevent Undercut Welding Issues for Flawless Construction Outcomes
Efficiency and accuracy are extremely important on the planet of welding, where also the tiniest blemish can endanger the structural honesty of a made piece. One typical difficulty that welders face is damaging, a flaw that can lead and deteriorate a weld joint to costly rework. By understanding the source of undercut welding and executing effective methods to avoid it, welders can raise their craft to new levels of quality (Preventing weld undercut). In the pursuit of remarkable fabrication outcomes, mastering the art of welding to prevent undercut problems is not simply a skill however a necessity for those aiming for excellence in their work.
Comprehending Undercut Welding
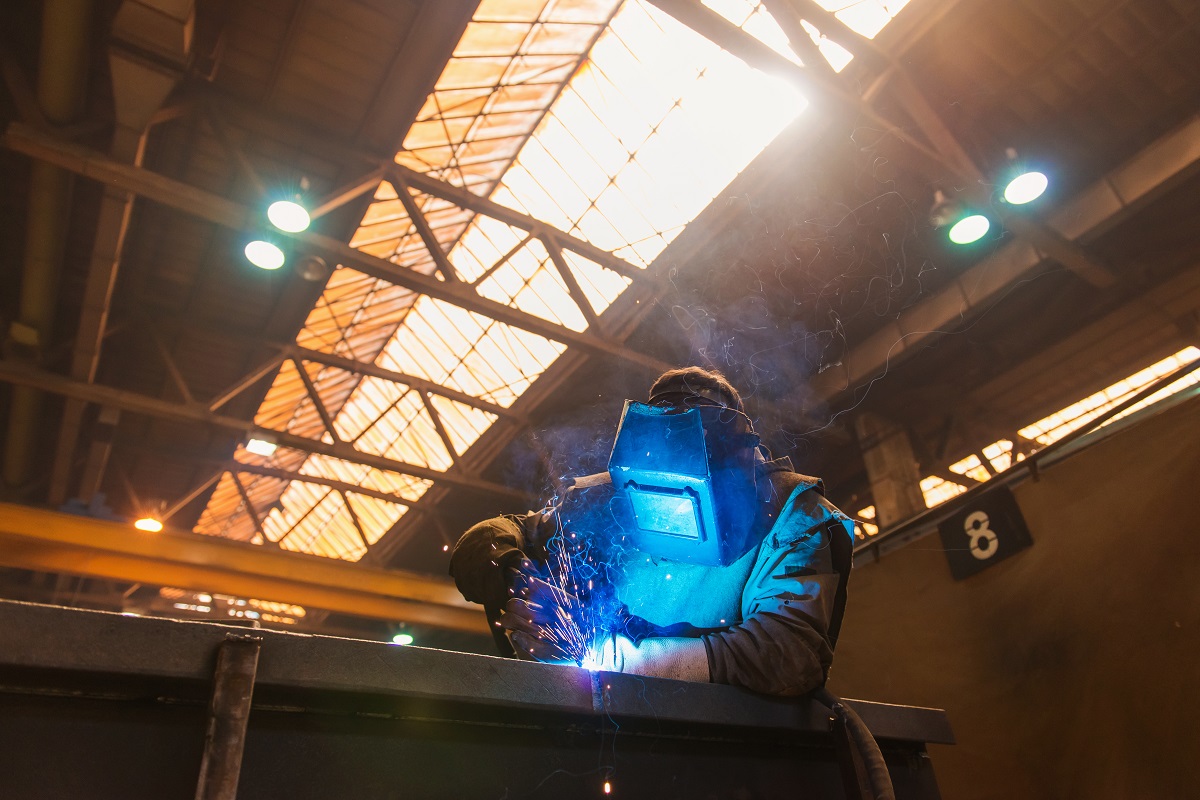
To stop undercut welding, welders need to make certain proper welding specifications, such as readjusting the present, voltage, travel speed, and preserving the correct electrode angle. Furthermore, making use of the appropriate welding technique for the specific joint setup is necessary. Utilizing weaving movements or backstepping techniques can assist guarantee proper weld steel deposition and lower the likelihood of undercut formation. Regular evaluation of welds during and after the welding process is also essential to catch any kind of undercut early and make essential changes to avoid further flaws. Preventing weld undercut. By recognizing the reasons for undercut welding and carrying out preventative measures, welders can achieve top quality, structurally sound welds.
Sources Of Undercut in Welding
Comprehending the factors that contribute to damage in welding is crucial for welders to create high-grade, structurally sound welds. Insufficient welding inaccurate or existing welding speed can likewise add to damage. Comprehending these causes and executing correct welding strategies can help stop undercutting issues, guaranteeing solid and sturdy welds.
Methods to avoid Undercutting

To minimize the threat of damaging in welding, welders can employ strategic welding methods targeted at improving the top quality and honesty of the weld joints. One effective approach is to readjust the welding parameters, such as voltage, current, and travel speed, to guarantee correct heat input and deposition. Maintaining a suitable electrode angle and guaranteeing consistent travel rate can additionally aid protect against undercut. In addition, making use of the proper welding great post to read technique for the details joint arrangement, such as weave or stringer grains, can add to minimizing undercutting. Preventing weld undercut.
Employing back-step welding methods and regulating the weld bead redirected here account can additionally assist disperse heat equally and lessen the risk of undercut. Routine examination of the weld joint during and after welding, as well as carrying out high quality assurance procedures, can assist in discovering and resolving undercutting concerns promptly.
Significance of Correct Welding Criteria
Selecting and keeping suitable welding specifications is crucial for achieving successful welds with very little issues. Welding specifications describe variables such as voltage, current, travel speed, electrode angle, and shielding gas flow price that directly affect the welding process. These specifications need to be meticulously changed based upon the sort of product being bonded, its density, and the welding strategy used.
Appropriate welding criteria make certain the right amount of warmth is put on melt the base steels and filler product consistently. If the specifications are set expensive, it can result in extreme warm input, triggering burn-through, distortion, or spatter. On the various other hand, if the specifications are too reduced, insufficient blend, absence of penetration, or undercutting might occur.
High Quality Assurance in Welding Operations
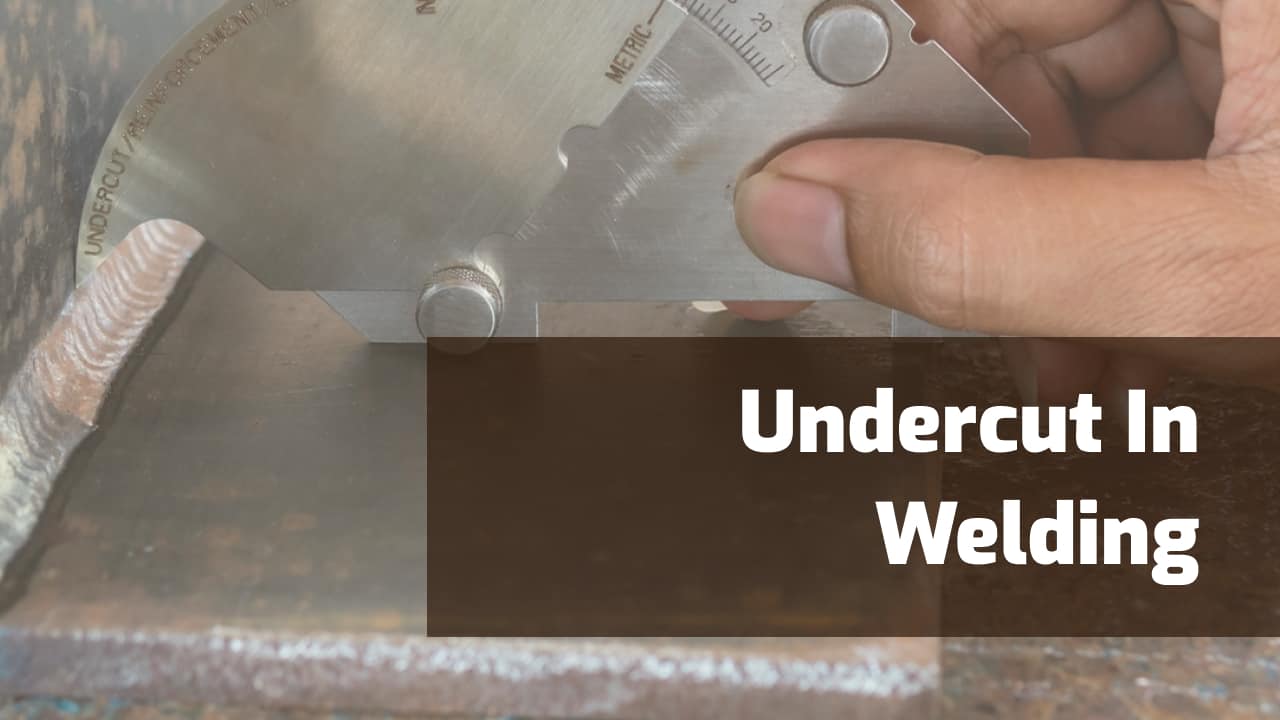
Final Thought
Finally, understanding the art of welding calls for a complete understanding of undercut welding, its causes, and techniques to avoid it. By guaranteeing appropriate welding parameters and implementing top quality guarantee practices, remarkable construction results can be accomplished. It is important for welders to consistently aim for quality in their welding procedures to avoid undercut concerns and produce high-grade welds.
Undercut welding, a typical defect in welding processes, occurs when the weld metal does not correctly load the groove and leaves a groove or anxiety along the bonded joint.To prevent undercut welding, welders must ensure appropriate welding parameters, such as changing the existing, voltage, travel speed, and keeping the appropriate electrode angle. Insufficient welding current or inaccurate welding rate can likewise add to damage.To reduce the danger of damaging in welding, welders can employ strategic welding strategies intended at enhancing the high quality and honesty of the weld joints.In verdict, mastering the art of welding requires a detailed understanding of undercut welding, its causes, and techniques to avoid it.
Comments on “Your Total Handbook to Preventing Weld Undercut Like a Pro”